|
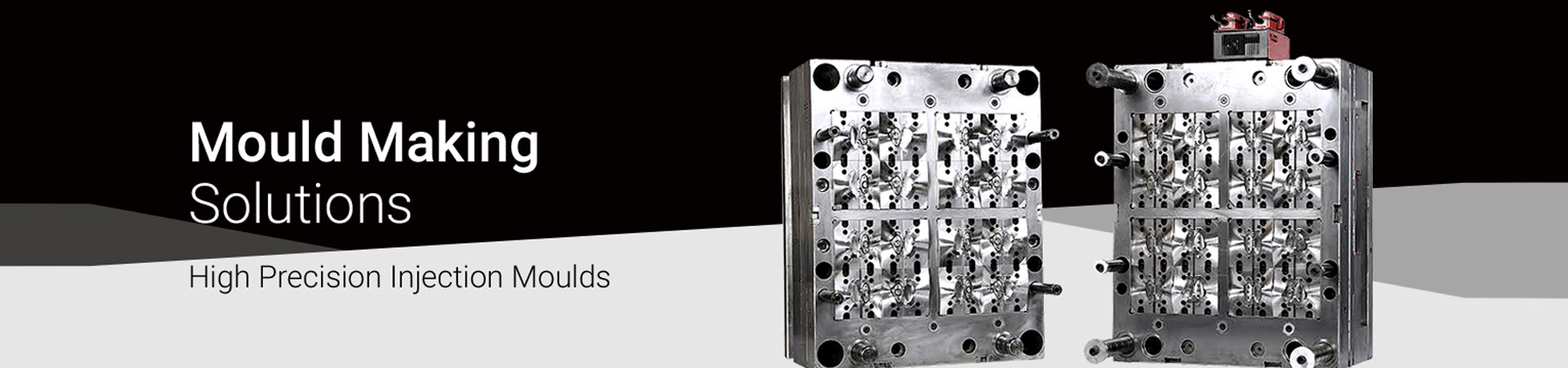
FAQs
Excellent Reputation And Highly Customer Recognition.
- How to get an accurate quotation?
- If you are interested in building moulds,please provide us with following info:
Drawings, photos or samples of plastic parts.
Detailed sizes of parts.
Material of parts.
Number of cavities.
Mould life required.
( the more detailed imformation provided, the more accurate the quotation offered)
- How long can I get the quotation?
- Normally, we can provide instant feedback and then provide quotation within 48 hours(Considering the time difference)
- What file format can you accept for my products?
- 2D, 3D are both available.
2D like PDF, CAD, JPG etc.
3D like STP, IGS, STL, SAT,PRT,IPT etc.
- Are you a manufacturer or a trading company?
- Truly we are a factory. We are a professional manufacturer, located in Shenzhen, China, with over 11 years’ export experience for machining precision parts & components and moulds.
- Is it possible to know how are my products going on without visiting your company?
- Yes. We will offer a detailed production schedule and send weekly reports with digital pictures.
- How can you ensure the quality?
- Every stage of our manufacturing process from initial start thorough to delivery has been monitored and controlled by QC. Measurements, inspections, tests and details are all documented and organized into reports for customer’s reference and records.
- Which Shipment way is available?
- By sea to your nearest port.
By air to your nearest airport.
By express (DHL, UPS, FEDEX, TNT, EMS) to your door.
As per your requirements.
- How do I know about the delivery?
- We will inform you of the tracking number once we get it from shipping agent. Also we will keep updating the latest shipping information for you.